The Royal Australian Engineers are renowned for their ability to solve problems and provide ‘work-arounds’ to obstacles and hazards during both peace and war. Whilst not unique to this particular corps, the application of innovative ideas requires tempering with qualified, trained and experienced consideration, and assessment of risks, even in a combat situation.
Over the past 30 years, the Australian Defence Force (ADF) has been involved in operations and exercises that saw our capabilities stretched, strained, and tested. While our soldiers, sailors, and aviators generally met or exceeded the task, it was not always due to being in location with all the manning, equipment, training, time, and resources readily available. On many occasions, the members directly involved were able to achieve the task via non-traditional processes and acts, dabbling within the grey area of approved and accepted procedures to achieve the mission.
Challenges to mission achievement have occurred throughout history, with notable parallels able to be drawn to previous conflicts within our home region. In post-World War II (WWII) reporting by the US Army, nine common issues occurred in most Southwest Pacific operations, three of which are as follows:
- tremendous distances involved, in both combat and supply operations
- continual critical shortages of construction forces and materiel
- continuing necessity to improvise.[1]
Although there has been economic and infrastructure development across Indo-Pacific nations since the conclusion of WWII, the majority of issues identified in post-War US Army reporting remain. Further challenges include increasing equipment size and complexity, available shipping space and load priority, as well end-location resource availability. Though pre-positioning and caching of non-perishable materials in regional centres may be an option in case of a contested environment, the paramount necessity to improvise remains as important today as it was in the past.
Knowledge, experience and necessity
"Lots of ingenuity gets you through times with no money better than money gets you through times of no ingenuity." – Terry Pratchett
Internal and external influences make every task bespoke, and a level of improvisation will always be required. Although borne out of necessity, improvisation and ingenuity require qualification, training, and experience to ensure that any alternative methods being applied meet the identified requirements as safely as possible. It is in this space that the ADF multi-tool thrives: the corps of the Royal Australian Engineers (RAE), aka the Sappers.
Sappers “conduct the dangerous, dirty, and demanding tasks that enable the Joint Force to live, move and fight”.[2] Although spread across a wide range of skillsets and specialisations, Sappers are renowned for their inherent “Sappernuity”. Sappernuity is “... knowing what needs to be done, and doing it, often under fire… .is practical and pragmatic, yet imaginative and inspired, ingenious in the face of adversity and ingenious in the glare of authority…. is what happens when the impossible meets the indomitable and the unfeasible encounters the imperturbable.... a blend of psychology, kidology and technology... is all of this, wrapped up in the scruffiest fatigues, a weary smile, a nod and a wink.”[3]
However, problem-solving skills are neither unique to sappers nor restricted to a particular trade, capability, or even service. Agnostic to background and driven by a broad spectrum of influences, ingenious and innovative solutions can and do solve problems to enable the success of a task. Nevertheless, creative solutions can also prove hazardous where personnel are unable to mitigate the risks of implementing a non-standard or unapproved method so far as reasonably practicable (SFARP).
So, what is SFARP?
The Work Health and Safety Act 2011 introduces the SFARP requirement for the management of risks, where a person conducting a business or undertaking is required:
- “to eliminate risks to health and safety, so far as is reasonably practicable; and
- if it is not reasonably practicable to eliminate risks to health and safety, to minimise those risks so far as is reasonably practicable.”[4]
The Act further defines reasonably practicable and how it pertains to works and actions that are or were at a particular time “reasonably able to be done in relation to ensuring health and safety, taking into account and weighing up all relevant matters”. According to the Act, relevant matters include but are not limited to:
- likelihood of the hazard or risk and the degree of harm that might result;
- what the person concerned knows, or ought to reasonably know, about the hazard or risk and methods elimination or minimisation;
- the availability and suitability of ways to eliminate or minimise the risk; and
- after assessing all of the above, the cost associated with eliminating or minimising the risk, including whether it is disproportionate.
Although SFARP is often incorrectly explained as “dodgy but safe”, in simplistic terms it is a:
- safe, temporary solution until the logistics chain provides the correct item.
- risk-mitigated, certified, and accepted variation from established standards.
SFARP enables the end-state to be achieved without having the exact elements required. Imagine attempting to complete a jigsaw puzzle without all of the pieces. An incomplete picture remains; however, you can identify the missing pieces and are able to finish the puzzle using alternate cut-to-shape pieces. Yes, the picture differs from the one on the box, but it is now complete.
Importantly, to deem that a task is complete SFARP, a person is required to have the appropriate qualification, training, and experience (QTE). Where subsequent residual risk remains beyond the persons’ ability to provide mitigation and it is reasonably practicable to do so, you must seek guidance and authorisation through technical reach back to a suitably qualified subject matter expert.
In times where a situation at a certain point may require assumption of higher risk levels, it still will need to be a defensible decision; evidence detailing that all possible efforts were made to address the outstanding safety risks SFARP are required. In all cases where residual risk remains, these must be continually reviewed and addressed where new means become available.
Ingenuity and improvisation in action
"Second, I believe in human ingenuity – that when we decide on a task to be done, no matter how daunting it may seem at the beginning, we are able to unleash human ingenuity and human innovative capacity that was unknown, and takes us to a solution." – Christiana Figueres
Ingenuity may be required to overcome issues in all aspects and situations whether temporary or permanent; it may affect the whole force, a sub-unit, a fleet of equipment, an installation, or even an administrative process or capability. In the following tables are four examples of ingenuity and improvisation that addressed morale and hygiene, infrastructure repair, minefield clearance and maintenance of operational installation requirements, all generally safe SFARP at that point and time.
The “Johnson” Shower, Hazebrouck (France), WWI[5] |
During salvage operations at Strazeele (sic) in July 1918, CSM James Johnston, 1st Field Company Engineers, had the idea to create a mobile shower for his company using materials left behind by the retreating German forces. The shower weighed approximately 40 lbs (18kgs) and provided hot or cold water using ‘a minimum amount of fuel and water’. The shower was constructed in the field in July 1918. The shower enabled eight men to be showered in three minutes, and it “proved a great boon to the entire Company”.[6] |
Extinguishing the oils wells of Seria, Borneo, WWII[7] |
In June 1945, the retreating Japanese set fire to 38 oil wells at Seria in Borneo. A platoon of the 2/3 Field Company was tasked to deal with the fires and repair the destroyed oilfield infrastructure. Using mostly improvised methods, the fires were extinguished within three months. The improvisations used included: a. being shrouded in wet blankets with a pitchfork welded to a length of pipe to close the valve b. using improvised heat shields, teams could get closer to the wells with hoses and equipment c. working alongside an American fire-fighting crew using a specialised isolating stack craned onto the well, its top removed with a round from a 2-pound anti-tank gun. |
Barrier minefield clearance, Vietnam War |
Sappers of the 1st Field Squadron RAE and Craftsmen from the Royal Australian Electrical and Mechanical Engineers, modified three M113A1s to assist in clearing anti-personnel minefields around the main Australian base at Nui Dat.[8] The largest minefield to be cleared was the 100-metre-wide, 11-kilometre-long Barrier Minefield located in the southern part of Phouc Tuy Province. This consisted of over 21,000 M16 “Jumping Jack” Anti-Personnel landmines, some with explosive anti-lift devices fitted. Eighteen Sappers were killed or wounded laying this minefield.[9] The APCs, named Her Majesty’s Armoured Personnel Carrier (HMAPC) Flint, Steele and George were fitted with additional blast-deflection plates and a modified axle. The extended axle was fitted with truck tyres to act as a roller that would cause the mines to detonate behind the APC as it drove past. At the time of use, “it was decided that the safest method was to detonate the mines under controlled conditions”.[10] |
Critical installation power control, Middle East Area of Operations (MEAO) |
Within the Middle East Area of Operations, an Australian base was established within an existing facility. The repurposed facility lacked critical power control switching that would affect operations at the base whenever the town power supply failed. As there was no applicable changeover switch readily available, the licenced RAE electrician manufactured a temporary changeover switch that consisted of two standard main switches mounted side-by-side, one upside down, with the switch bails joined. The switch was tested for correct operation and electrical safety and was deemed by the electrician to be as safe SFARP; subsequently installed, the switch remained in operation until the logistics chain was able to provide the correct item. |
Invigorating ingenuity in our personnel
“Soldiers can sometimes make decisions that are smarter than the orders they've been given.” – Orson Scott Card, Ender’s Game
Although this article focusses mainly on the Australian Army’s amazing, remarkable, well-mannered, and modest sappers, ingenuity and innovation are not restricted to a particular trade, mustering, capability, or even service. Our soldiers, sailors and aviators are doing the business and are well aware of procedural issues and process rub-points, and thus they may be doing workarounds on a daily basis – i.e. normalised deviation that is particularly dangerous at the lower levels.
As leaders, managers, and supervisors we must ensure that any normalised deviation is stopped immediately. However, before carrying out the knee-jerk reaction of reviewing what punishments you can impose on the member or members involved, pause and ask questions such as the following:
- Why has this occurred?
- Are required outputs being met?
- Is the deviation from the norm still safe SFARP?
- Are changes needed to make the process safer and more efficient?
- If possible, how do we apply changes where required?
Ingenuity and innovation suggestions need to be taken seriously and not dismissed immediately. All personnel should be encouraged to come forward and highlight issues with current equipment, methods, and processes. Listen and provide guidance – give them support and trust them to try alternate methods and processes, with appropriate oversight and guidance. Once tried, if it does not work then it is not necessarily a failure, but a lesson. We should not be afraid to attempt things that may not work initially.
The ADF has a very diverse workforce with many differing experiences and ideas. If we are to be a truly agile force, we need to tap into this knowledge and base of experience. Current and past solutions may not work with new training regimes, equipment, and the latest generations of recruits. Step back and be open to new ideas and new ways of doing things. However, the value of past lessons-learnt should not be forgotten nor dismissed as many were hard-won and may have occurred during times of low technology and limited available resources.
For those ingenuity and innovation champions with ideas, whack your hand up in the air. Remember though, your idea must be fair dinkum and not “we need slushy machines with two flavours in the gym because I get hot in there”. Identify the issue, explain the problem, and suggest a feasible solution. Examples of ways to be heard and considered include approaching your chain-of-command, submitting an enhanced-capability Report on Defective of Unsatisfactory Material (RODUM), and contacting or visiting your local Army Makerspace.[11]
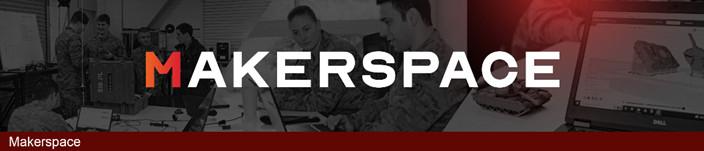
The Final Word
“What the Anzac legend did do, by the bravery and sacrifice of our troops, was reinforce our own cultural notions of independence, mateship, and ingenuity. Of resilience and courage in adversity” – Paul Keating
The ability to provide a safe, workable solution with a level of known mitigated risk is paramount. While there will be times when extreme risks need to be taken with likely and accepted consequences, it still will need to be a defensible decision regardless of the security threat. Consider obstacles with fresh eyes and methods, but do not dismiss previously learned lessons nor out-of-the-box ideas from unit members. Furthermore, do not be afraid of the possibility of something not working on the first attempt – that is a learning point not a failure. Trust your soldiers, sailors, and aviators – they are valuable assets and their input should not be ignored.
Acknowledgments
MAJ Sita Norsworthy
WO1 Andrew Beaman
WO1 Greg Buckley
WO1 Golborn Turner
Mr Andrew Sibraa
End Notes
[1] Book, Engineers of the Southwest Pacific, 1941-1945, Volume VI, Airfield and Base Development, Major General Hugh J Casey, Chief Engineer, 1951.
[2] Article, RAE Vision, Australian Sapper 2018_eVersion.pdf, BGDR David Wainwright DSC, 2018
[3] Book, A Sappers’ War: How the Legendary Aussie Tunnel Rats Fought the Vietcong, Jimmy Thomson with Sandy MacGregor MC, 22 August 2012
[4] Legislation, Work Health and Safety Act 2011, Part 2, Division 1 and 2, Federal Register of Legislation - Work Health and Safety Act 2011, 23 July 2024
[5] Article, Australian Engineers in the First World War, Australian Engineers in the First World War, Australian War Memorial, Alessandra Antonello, 21 January 2009
[6] Article, The Johnston Shower, 1st Feld Company Engineers, The Johnston Shower, 1st Field Company Engineers, aussiesappers.wordpress.com, Vance Kelly, 19 February 2016
[7] Images(Public), AWM109965/113642/113644/113645/113653/113654/113666/11380, Google search - AWM images - Seria Oil Wells, AWM Collection, 01 August 1945
[8] Images, AWM PO4665.089/PO4665.090/PO4665.094/PO4665.116/PO4665.118/ PO4665.124/PO4665.130, Google Search - AWM Images - HMAPC Flint/Steele, AWM Collection, 21 July 1969
[9] Article, Laying the Barrier Minefield: The Consequences of a Fatally Flawed Decision, HOLDFAST Newsletter, https://tunnelrats.com.au/pdfs/newsletters/Holdfast-34.pdf , “Jethro” Thompson, Joe Cazey, Peter “Roo Dog” Scott, July 2019
[10] Article, Australian Army Museum of Military Engineering (AAMME), Australian Sapper 2011 eVersion.pdf, MAJ Rob Petrenko, 2011
[11] Website, MakerSpace, Pages - Army MakerSpace, QINETIQ, 07 February 2023